서론 - 전고체 셀 구조 최적화는 실리콘 음극재 상용화의 열쇠
전고체 배터리(All-Solid-State Battery, ASSB)는 액체 전해질 기반 리튬이온전지를 대체할 고에너지 밀도·고안전성 전지로 주목받고 있다. 실리콘(Si) 음극재는 이론용량이 3,579 mAh/g로 흑연보다 약 10배 높아 차세대 전지의 핵심 소재로 부상했지만, 전고체 시스템 내에서의 적용은 단순한 소재 대체만으로 해결되지 않는다. 실리콘은 충방전 과정에서 최대 400%에 달하는 부피 팽창을 겪으며, 고체 전해질과의 계면 박리, 전극 밀도 불균형, 기계적 응력 집중 등의 복합적인 문제를 유발한다.
이러한 문제는 셀 구조 전체에 영향을 미치며, 전극층의 구성, 집전체 설계, 압력 분포, 계면 일체화 기술 등 다양한 요소가 유기적으로 설계되지 않으면 실리콘의 고용량 이점을 활용할 수 없다. 본문에서는 실리콘 음극이 전고체 전지에 안정적으로 적용되기 위한 구조적 설계 최적화 방안을 정리하고, 국내외 실험 결과를 기반으로 셀 구조의 주요 변수들이 배터리 성능에 미치는 영향을 정량적으로 분석한다.
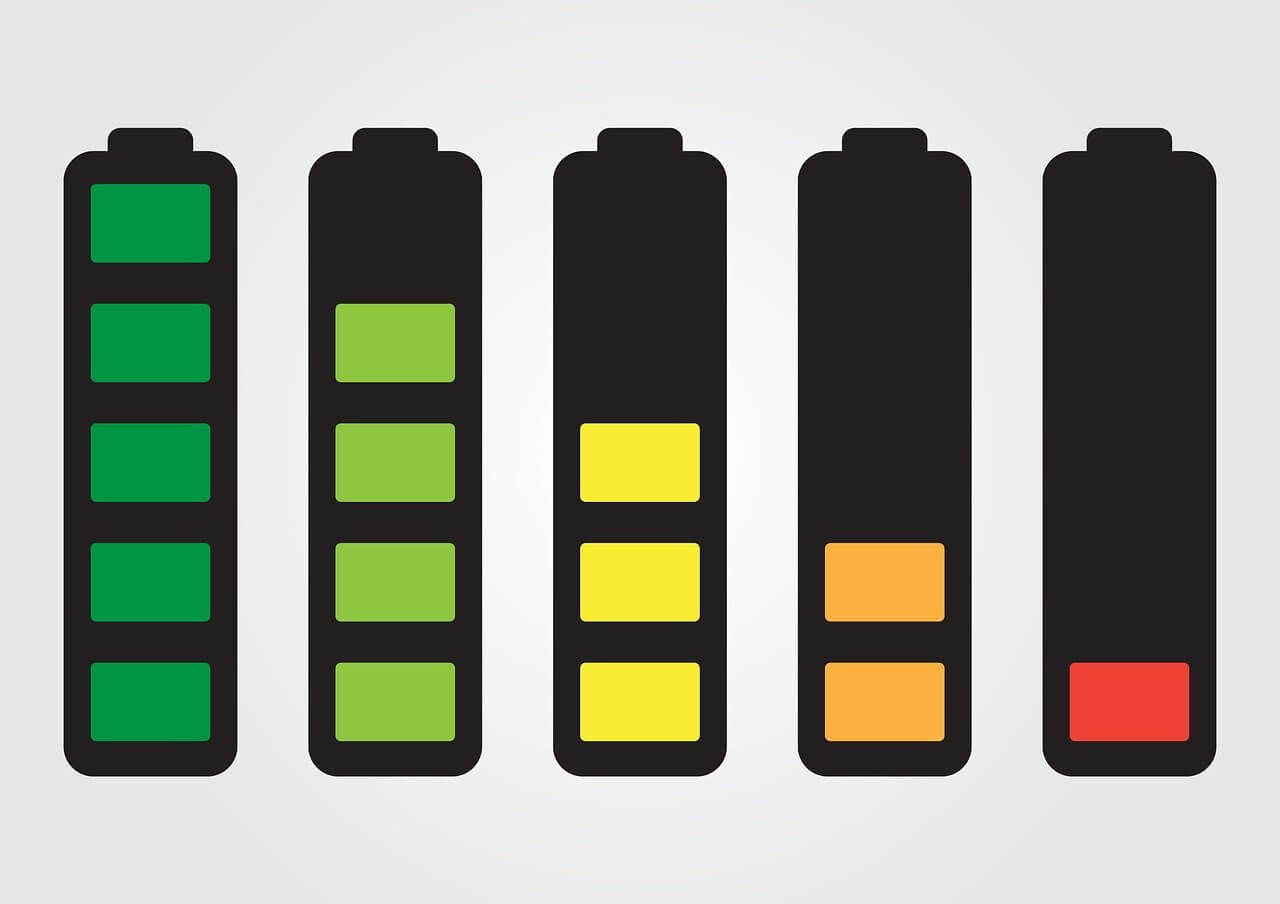
1. 전고체 셀 내 실리콘 음극 구조의 주요 설계 변수
전고체 셀에서 실리콘 음극재의 안정성과 출력 성능을 좌우하는 구조적 변수는 다음과 같다.
- 전극층 조성비(Si:Carbon:Binder 비율)
- 전극 압축 밀도 및 두께
- 고체 전해질 분산 균일도
- 집전체(Collector)의 표면 처리 및 구조
- 전체 셀 압력 유지 시스템 설계
이들 요소는 단순한 소재 조성 문제가 아니라, 셀 구조적 일체성과 직접 연결되어 있으며, 각각의 변수들이 유기적으로 작용해야 실리콘 음극의 싸이클 성능과 Coulombic 효율을 유지할 수 있다.
도식 1. 실리콘 음극 중심의 전고체 셀 구조 개요
[집전체] - [실리콘 복합 전극층] - [고체 전해질층] - [양극] - [집전체] ↑
전극층 내 고체 전해질 분산, 전도성 부여, 균일 압축 필요
2. 실리콘 음극 조성비 및 전극 밀도의 영향
전극의 조성비와 압축 밀도는 셀의 용량과 구조 안정성에 결정적 영향을 미친다. 실리콘 비율이 높을수록 초기 용량은 증가하지만, 싸이클 수명은 짧아지는 경향을 보인다. 반면 탄소나 바인더 함량을 증가시키면 구조적 안정성은 확보되나, 용량 밀도는 감소한다.
실험조건
- 음극 조성비: 실리콘(CVD Si) : 탄소 : 바인더
- 바인더: CMC/SBR (수계)
- 압력: 150 MPa
- 전극 두께: 80 μm
- 싸이클 횟수: 100회
표 1. 실리콘 음극 조성비에 따른 성능 비교
80:10:10 | 3,120 | 54.1 | 96.8 | 31.2 |
70:20:10 | 2,860 | 65.5 | 97.9 | 24.8 |
60:30:10 | 2,560 | 76.8 | 98.7 | 18.5 |
해당 결과는 실리콘 비중이 높을수록 에너지 밀도는 증가하나, 팽창률과 계면 박리가 심화되어 싸이클 수명이 급격히 떨어짐을 보여준다. 따라서 70:20:10 비율이 실용성과 고용량 간의 최적 절충점으로 판단된다.
3. 전극 내 고체 전해질 분산 균일도와 계면 밀착성의 상관관계
전고체 시스템에서는 전극 내부에 고체 전해질이 균일하게 분포해야 이온 통로가 형성되고, 실리콘 입자 간 전기화학적 연계성이 유지된다. 분산 균일도가 떨어지면 국부적인 이온 고갈 및 응력 집중으로 인해 미세 크랙이 발생하고, 결국 전체 전극의 계면 안정성이 붕괴된다.
실험 - 고체 전해질 분산 방식에 따른 성능 차이
- SE: Li₆PS₅Cl (황화물계, 10 wt%)
- 분산 방식: 고속 혼합 vs 저속 교반
- 공정: 슬러리 도포 → 건조 → 압축
표 2. 고체 전해질 분산 방식에 따른 싸이클 성능
고속 혼합 | 92.4 | 2,950 | 68.2 | 175 |
저속 교반 | 74.1 | 2,910 | 52.6 | 262 |
분산 균일도가 높을수록 싸이클 후 성능 유지율이 높고, 계면 저항 증가 폭도 작았다. 이는 고체 전해질이 전극 전반에 고르게 분산되었을 때 실리콘의 부피 변화가 구조 전체에 균등하게 작용하기 때문으로 해석된다. 분산 기술은 단순한 공정의 문제가 아니라, 셀 안정성을 좌우하는 핵심 설계 요소이다.
4. 집전체 설계와 전극 접합력의 역할
전극은 집전체(Current Collector)에 밀착되어 있어야 전류가 안정적으로 흐르고, 충방전 중 발생하는 기계적 스트레스를 지지할 수 있다. 실리콘 음극은 팽창률이 크기 때문에, 집전체 표면의 마이크로 구조나 코팅 기술이 매우 중요한 요소로 작용한다.
실험 - 집전체 표면 상태에 따른 실리콘 음극 전극 밀착도 비교
- 집전체 재질: 구리(Cu)
- 표면 처리: (1) 무처리, (2) 나노거칠기 처리, (3) 카본 코팅
- 측정 항목: 전극 접착력(N/cm), 싸이클 안정성
표 3. 집전체 표면 처리 방식에 따른 접착력 및 싸이클 성능
무처리 | 2.3 | 48.7 | 95.6 |
나노거칠기 처리 | 4.8 | 63.4 | 97.4 |
카본 코팅 | 5.6 | 69.8 | 98.1 |
접착력이 높을수록 계면 박리 현상이 줄어들며 싸이클 수명도 향상되었다. 카본 코팅은 전도성 향상과 함께 기계적 완충층 역할도 겸할 수 있어, 실리콘 음극 전극과 집전체 간 계면 신뢰도를 크게 높이는 것으로 나타났다.
5. 전체 셀 압력 유지 시스템과 구조 안정성
전고체 전지는 운용 중에도 일정 압력이 유지되어야 고체 전해질과 전극 간 접촉이 지속될 수 있다. 실리콘 음극은 팽창/수축을 반복하기 때문에 일정한 압력 유지가 특히 중요하다. 이를 위해 셀 케이스 내장형 압축 시스템, 가변 지지 구조, 스프링형 구조 등이 적용되고 있다.
실험 - 셀 압력 유지 여부에 따른 성능 변화
- 압력 조건: (1) 고정압(150 MPa), (2) 무압 상태
- 셀 구성: Si(70%) 복합 음극 + 황화물 전해질 + NMC 양극
- 충전 조건: 0.1C, 상온
표 4. 압력 유지 여부에 따른 실리콘 음극 ASSB 셀 성능
고정 압력 유지 | 2,980 | 71.2 | 19.5 |
무압 상태 | 2,920 | 42.3 | 47.1 |
압력이 유지되지 않는 경우, 실리콘의 팽창에 의한 계면 분리 및 전극 변형이 누적되어 급격한 성능 저하가 발생하였다. 반면 일정한 압력이 유지된 경우, 계면 접촉이 안정적으로 유지되며 용량 유지율과 내부 저항 모두 양호한 수치를 나타냈다.
결론 - 실리콘 음극 기반 전고체 전지 셀의 구조 설계는 통합적 접근이 필수이다.
실리콘 음극재는 전고체 배터리에서 고용량화를 위한 유력한 선택지지만, 그 적용은 단순한 소재의 문제를 넘어 전극층의 조성, 고체 전해질의 분산 방식, 계면 접착력, 압력 유지 구조 등 복합적 구조 설계가 수반되어야 한다.
본 분석에서 확인된 핵심 인사이트는 다음과 같다.
- 실리콘 함량과 싸이클 수명은 반비례 관계를 가지므로, 복합재 설계와 균형점이 중요하다.
- 전극 내 고체 전해질 분산 균일성은 계면 안정성과 직접 연결되며, 고속 혼합 등의 공정 제어가 필수적이다.
- 집전체 표면 처리는 전극 계면 신뢰성을 높이는 결정적 요소이며, 탄소 코팅이 유리하다.
- 셀이 일정한 압력을 유지하도록 설계되었을 때, 실리콘의 팽창을 효과적으로 제어할 수 있다.
결론적으로, 실리콘 음극이 전고체 시스템에 성공적으로 적용되기 위해서는 소재·전극·셀 구조·공정의 유기적 통합 설계가 필요하며, 이러한 구조 설계 역량이 미래 전고체 배터리 경쟁력의 핵심이 될 것이다.